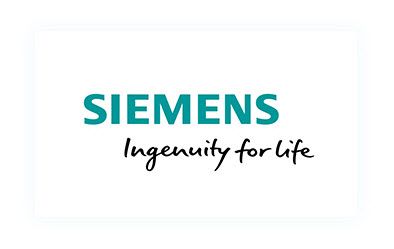
The Reliable Silent Industrial Controller.
New Zealand manufacturers want to produce their products day in and day out without having to know what is under the hood of their manufacturing machinery. They want to focus on producing great products consistently and then selling them to the good folks of New Zealand and the world.
Siemens controllers have unrivalled reliability, working year in and year out without raising their heads. They are so reliable that their owners often don’t even know they are Siemens, as they never have to concern themselves with them. They are the silent, efficient backbone of a huge number of New Zealand’s manufacturing enterprises.
Feature-Rich Siemens Controllers
“But wait! I want world-class manufacturing equipment so I can be competitive within New Zealand and against international competitors. I want to maximise my machinery productivity, so now I care about my underlying manufacturing control technology.”
Siemens Controllers, whether PLCs, Industrial PCs, Motion Controllers, or Sinumerik CNC controllers, have an unrivalled value proposition. This value is driven by the largest feature stack on the market, combined with the broadest range of industrial automation equipment to connect them to of any industrial automation manufacturer in the world.
The features include core enablers of ‘industry 4.0 style production’, including:
1. Big Data capture
2. Cloud analytics, visualisation and insights (to industrial security standards)
3. Edge processing, including analysis to inform preventative maintenance strategy for the mechanical drive train of your manufacturing machinery.
4. The broadest and deepest industrial ethernet-based networking architecture in the industrial automation market.
5. Your Siemens controllers can support a wide array of networking and communication protocols, aiding interoperability and data gathering.
6. Easy methods of calculating OEE or other KPI data and porting them to platforms to facilitate NZ manufacturing management decisions.
Siemens Controllers Facilitate Easy Maintenance
Let’s face it, no matter how reliable the PLC is, machinery breaks down occasionally: sensors get knocked, wires get damaged, gearboxes wear out, and bearings collapse.
Siemens controllers are programmed in Siemens’ TIA Portal. The TIA Portal is a single point-of-truth system that handles the setup and configuration of the largest array of Industrial Automation Equipment of any Industrial Automation vendor. All your PLCs, Motion Controllers, Safety Systems, I/O, Variable Speed Drives (VSDs / VFDs), servo drives, HMI (visualisation screens), SCADA, smart and redundant 24VDC power suppliers and networking equipment (wired and wireless) are configured in this one platform—all referencing the same TIA Portal database. Therefore, if there is a fault in your machinery, the maintenance technician only needs one piece of software to diagnose it and have visibility across every part configured in it with a few clicks of the mouse. Therefore, if all the automation equipment in your production machinery is Siemens, one can glide through the TIA Portal, read the integrated diagnostic messaging system across all equipment and quickly check for any automation part or networking faults. Once the user is sure there are no issues on the automation hardware front, they can focus on checking Siemens controller logic for what is holding up their production machinery.
Siemens controllers combined with Siemens Unified Comfort HMIs have the powerful option of “ProDIAG”. Your machinery/production line OEM or your trusted Siemens automation service specialist (Such as CNC Design Ltd) can configure ‘supervisions’ within the controller code. If the code gets stuck at these supervision points, ProDIAG can display the relevant section of the controller code on the HMI—so the user can see what condition the controller is waiting for. This aids in super fast diagnostics, as one does not need to get out or start a programming computer to check the system. In fact, switched-on operators can view the ProDIAG HMI screens and see what is stopping the machine. Often, it is as simple as a sensor not registering due to being knocked and now misaligned, a product jam stopping a sensor from clearing, or a safety gate not being closed fully—simple issues operators can often fix themselves. Therefore, ProDIAG de-skills machine diagnostics to speed up identifying and rectifying interlock and process issues.
Siemens Controllers—Pioneering Safety Controllers
Siemens was one of the first companies in the world to combine safety controllers with standard logic controllers (PLCs) in one device. By 2007, Siemens “Safety PLCs” were well-embedded in the world market via the Simatic S7300 range. Over the intervening years, their safety performance has been proven beyond all doubt. This safety technology has been incorporated into Siemens’ industrial PCs and Sinumerik CNC Machine controllers in this period. It is now in its second major revision as part of S71200 and S71500 PLC technologies, which are embedded into Industrial PCs and CNCs in ‘soft PLC’ format. New Zealand manufacturers benefit greatly from Siemens safety controller technology, as it massively increases transparency in the safety system. If anything doesn’t work as expected in the safety system, the safety PLC can report on that immediately for rapid rectification. This gets manufacturing plants up and running again in as little time as possible. Traditionally, using safety relays, an electrician or technician would have to carefully work through every wired signal individually to ensure it was propagating the expected signal correctly. Modern safety PLC-based system report immediately. “Short circuit on input 43.0—Machine control panel e-stop button”, or broken wire on the same, etc. Then, the manufacturer’s maintenance team can rectify issues quickly, returning manufacturing machinery to production and making money.
Siemens safety controller technology allows for the configuration of nuanced safety systems. In the past (using safety relay technology), there may have been times when effective safety evaluation could not be employed. With intelligently deployed safety PLC-based systems, one can monitor all movements and states of a machine in any mode. For example, more complex machines often need humans to work within their guarding during setup. Still, a safety PLC can monitor such situations to lower risk to as low as reasonably practical. For example, monitoring that while an axis is still enabled, it does not move during setup. Or that it only moves at a slow speed, hence reducing risks. Or the axis can only move in one direction, away from the person setting it up.
Siemens Controllers Enable Remote Maintenance
The highly networked Siemens Controllers, with their auxiliary industrial automation systems within the TIA Portal, facilitate effective remote maintenance. If a New Zealand manufacturer chooses Siemens Controllers for their manufacturing machinery, their machinery OEM or their New Zealand-based trusted Siemens service partner (such as CNC Design) can remotely log into their machinery to diagnose it. This is usually done via the customer VPN, but Siemens NZ can supply a Scalance 5G cellular-based system to facilitate remote access. In this way, you can get expert OEM or service partner assistance with no travel time. Even if you are in an area of New Zealand away from your expert Siemens service partner or your OEM, the power of the TIA portal and highly networked equipment means there is no difference for the service technician between being plugged directly into the machine or connecting to it remotely.
Specify Siemens Controllers for Your Next Manufacturing Machine
CNC Design, New Zealand’s longest-serving and most specialised Siemens expert, can assist you with specifying the automation hardware for your next machine purchase. We can review what the OEM is suggesting to ensure you are getting current-generation parts with the longest life span—reducing your overall cost of ownership. CNC Design can then assist you with maximising your uptime and minimising unforeseen breakdowns during the life cycle of your machinery. From expedited spare part supply to expert consulting and optimisation services to add value to your manufacturing machinery—call CNC Design.