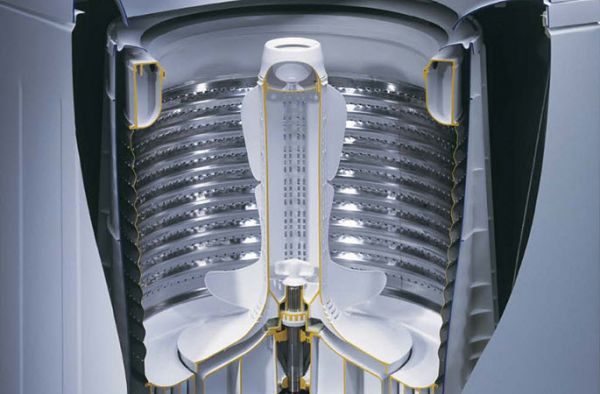
Client: Production Machinery Limited
Industry: Household appliance manufacturing
Project: Designing automation technology for manufacturing appliances
Manufacturing world-leading appliance lines for Fisher & Paykel
Production Machinery Limited (PML) specialises in building assembly lines for the manufacture of domestic appliances.
“We build the machines that build the machines, from concept all the way through to production,” explains Rob Craigie, PML’s Business Development Manager. “We started as a Fisher & Paykel division, and while still owned by F&P, we now mainly supply lines to offshore clients, including other world-leading appliance companies.”
The challenge: producing flexible assembly systems
Starting out in the low volume New Zealand market meant that PML had to produce very flexible assembly lines that could quickly be adapted to produce different products. In today’s marketplace, where appliances have shorter lifecycles, this kind of flexibility is in high demand. Rob says: “We build custom-made, versatile machines. It’s a very competitive business and to succeed we need a reliable partner – like CNC Design – who delivers innovative and creative technologies. Every product line is different.”
CNC’s solution: an innovative approach for motor winding using Siemens CNC control
The traditional approach to this task would have been to use a PLC or motion controller, however CNC Design’s engineers chose a Siemens Sinumerik solution for CNC control. Along with other advantages, this solution gives the machine operator on-the-go G code programming capability.
Steve Honey, Project Manager at PML, one of the experts managing the manufacture of world class automated production lines under the brand Fisher & Paykel, trusts us to always select the best technology for the job.
“We could use other control hardware suppliers for Fisher & Paykel’s motor lines, but have selected to use CNC because they have proven skills and experience. All around, CNC provides a good turnkey package with world-class service and support. They’ve performed to target and they have met the schedule. In other words: they’re delivering exactly what we require. CNC has also been asked to participate in overseas commissioning and they’ve done so at a very realistic cost.”
Rob Craigie adds: “They take responsibility and offer a cost-effective, high quality service. They always deliver what they promise and meet tight deadlines. We’re happy with the results. We trust CNC and work collaboratively with them. They are very professional, open and honest, and have a very high standard of conduct and performance. We’ve been working with the CNC team for about 20 years now and there is likely to be more work for them in the pipeline.”
The result: world-leading machines for efficient manufacturing lines
“CNC has been instrumental in building stages for a number of appliance production lines over the years. They complement skills that we have in-house. Their technology and expertise help us build world-leading machines for our clients, which ultimately translates into export sales. That speaks for itself,” says Rob Craigie.