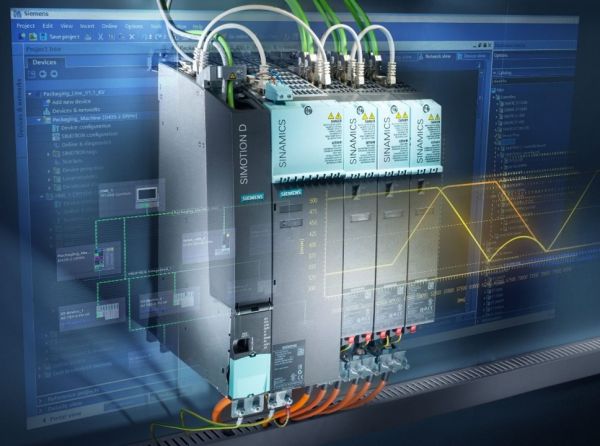
It’s important to choose an efficient architecture when designing a control system for your machine, whether it is a metal former, moulder, wrapper, depositor, or anything else. Architecture refers to the selection of controller, human machine interface (HMI), IO, drives, network components, computers, sensors and actuators, and how these are connected together.
For most machines, there are plenty of architectures that will work, but not all of them are ideal. For example, a low-featured PLC controlling a machine with complex motions might have a low hardware cost, but a high labour cost from writing the required code. Or, a high-feature PLC might be coupled with a high-feature drive system, where both can achieve a required motion function such as camming. In this case, you have to choose which device (PLC or drive) will do the job, leaving the other device not fully utilized.
One of the most important architecture considerations is the controller (e.g. PLC, CNC controller), because it is typically the nexus or ‘brain’ of the whole system – being the device that processes the inputs and outputs in real time. This article focusses on the controller. This doesn’t mean to say that you should select your controller without considering the other components and how they all fit together. The system should definitely be designed as a whole. But this article aims to highlight the features and benefits of different Siemens controllers, to show how each can fit productively into the overall solution.
We believe one of the biggest advantages from choosing Siemens is the range of options available, allowing you to construct an ideal solution. We’ll cover three types of controllers that are typically used in machinery with motion control requirements. CNC Design has extensive experience in specifying and supporting the implementation of all of these types of control systems.
· PLCs (from the SIMATIC range)
· Motion controllers (from the SIMOTION range)
· CNC controllers (from the SINUMERIK range)
The other side of the equation is the drive system. The drive system shares the automation task with the controller. In some cases, it may make sense to have a simple controller paired with complex drives that perform most of the motion functions (positioning, homing, synchronization, etc). In such cases, the drives receive high level commands from the controller, such as “move there,” “start synchronization,” etc. In other cases, it may be preferable to have a complex controller paired with simple drives, where the controller performs the complex motion tasks and issues simple speed commands to the drives.
PLCs
PLCs, being general-purpose in nature, are the most flexible at implementing a wide variety of automation tasks. However, the trade-off for this flexibility is that the control kernel and programming methods are not optimised for any specific task. So, while PLCs can implement more-or-less the same motion applications as other controllers mentioned in this article, code development will typically take longer. This needs to be factored into decision-making, especially for one-off or low-volume machines.
Siemens offers PLCs with a range of motion capabilities to suit each application, from simple speed control and single axis positioning, through to synchronizing dozens of axes and 6-axis safe kinematics. Why would you use a Siemens PLC to control a robot? You probably wouldn’t if the robot was a stand-alone device. But if it was a component in a larger machine with other automation requirements, it may make sense to control the entire machine (including robot) with a PLC.
S7-1200
FIGURE 1: Siemens Simatic S71200 PLC
The S7-1200 series of PLCs is a compact, high-featured PLC with limited memory and processing power. While it is possible to perform positioning control directly with a S7-1200 PLC, it is best paired with drives that handle the positioning control themselves (e.g. Sinamics V90, S120, G120 with Epos).
The motion capability of a S7-1200-based control system is effectively limited to what the drives can achieve. In the case of economic V90 drives, this is positioning and torque control. In the case of the S120 drive system, complex functions such as camming and synchronization and applications such as flying saws and cross cutters can be achieved with the DCC (Drive Control Chart) option.
In all of the above scenarios, the S7-1200 sends high level commands (e.g. position, length, speed, acceleration, torque, offsets, etc) to the drive system; so flexibility such as calculating cam profiles on-the-fly is difficult to achieve.
For applications with motion control, the S7-1200 often proves an economic and effective choice where:
· The number of axes is limited.
· The motion tasks do not require a high degree of flexibility.
· Any synchronization required can be achieved in the drive system (e.g. S120).
· The amount of ancillary (non-motion) processing required is not huge.
If DCC is being used, this is effectively a programming language, and the cost of development needs to be taken into account.
Like the S7-1500 series, the S7-1200 series supports remote IO, distributed safety and OPC UA.
S7-1500
FIGURE 2: Siemens Simatic S71500 PLC
S7-1500 is Siemens’ flagship PLC range. The two most common form factors are ET200SP, suited to small to medium sized applications, and ET200MP, suited to a range of applications from small to very large.
Unlike S7-1200s, S7-1500 CPUs have good capability with implementing motion tasks using Technology Objects. This allows complex motion functions to be achieved by pairing S7-1500 CPUs with simple and cost-effective drives such as V90 or S210. This shifts the burden of the higher level motion functions to the CPU, allowing the drives to simply provide tight speed/torque control. The motion programming is also performed in an IEC61131-3 style environment with PLCOpen type motion instructions – which requires more effort than with SIMOTION or SINUMERIK controllers, but is based on industry standards.
The following motion functions can be performed on S7-1500 standard CPUs:
· Positioning.
· Relative gearing.
· Output cams & tracks.
· High speed measuring inputs.
S7-1500T technology CPUs additionally provide the following functions:
· Absolute gearing.
· Synchronization to a real leading axis, e.g. a web encoder.
· Distributed synchronism.
· Camming.
· Kinematics (e.g. cartesian pickers, delta pickers, robot arms).
These capabilities allow a wide range of machines to be automated. CNC Design has implemented control systems based on the S7-1500T in machines such as flying saws and cross lappers. The engineering task is simplified by having all functions configured from one software package (TIA Portal) – HMI, PLC, drives and safety.
S7-1500 PLCs have all of the built-in features mentioned with S7-1200 above. S7-1500 PLCs also support, among other features:
· The advanced S7-Graph programming language.
· Prodiag for easy diagnosis of machine faults.
· Secure communication.
· Built-in diagnostics – automatic display of system faults on HMI devices.
Distributed Motion
Another important advantage of S7-1500 CPUs is Isochronous communication. Profinet IRT (Isochronous Real-Time) is an extension of the Profinet protocol that allows the parts of a motion control system to be distributed across an Ethernet network– for example, Profinet encoders, high speed remote I/O, and drives operating synchronously over Profinet. Unlike EtherCat, normal IP-based communication can also take place on an IRT-enabled network (e.g. for PLC-HMI communication, or programming), without additional communication adapters. Both IRT and non-IRT devices on a network can be accessed through standard tools such as ping, Proneta scanning, the devices’ web servers, and Siemens programming software.
Fail-safe (F) Option
FIGURE 3: Siemens Safety PLCs in IPC, ET200SP, S71500 and S71200 Form Factors
Most S7-1200 and S7-1500 CPUs have fail-safe versions. Fail-safe CPUs allow the machine safety functions to be implemented without the need for separate safety controllers such as Flexi Soft. The drive safety functions (STO, SS1, SBC, etc) are implemented over Profisafe, i.e. over the existing Ethernet network. There are several advantages to this approach:
· Only one CPU is required.
· The development is done with one software package (TIA Portal).
· Built-in diagnostics, e.g. with the Diagnostic Viewer in Simatic panels.
· Simplified architecture.
· Reduction in wiring (safety over Profinet).
Fail-safe Siemens CPUs are almost always used instead of standard CPUs, because of the points mentioned above, and because the price difference is very reasonable.
Simatics Drive Controller
FIGURE 4: Sinamics Drive Controller
This is a new S7-1500 controller in a S120 drive form factor. The Simatic Drive Controller combines IO, a Fail-safe technology CPU, and a drive control unit into one device. It is a good fit for mid-to-high complexity machines with constraints on cabinet space.
Software Controller
FIGURE 5: Siemens Simatic Software Controllers AKA IPCs AKA Industrial Computers running soft PLC
The S7-1500 Software Controller is a PLC runtime hosted on a Simatic industrial PC. The PLC and Microsoft Windows run on separate partitions. This ensures stability for critical tasks, but allows for close interaction between the PLC and Windows applications. The software controller is ideal for:
· Systems that require a direct connection between Windows software and the PLC (for example, image processing or saw cut optimization).
· Very large and/or high performance systems (up to 250 axes) – thanks to the power of the high-end Simatic PCs.
Motion Controller – Simotion
Figure 6: Simotion Motion Controller with Sinamics S120 Infeed & Motor Modules
When your application is mainly motion and includes dynamically calculated cams or large and complex motion sequences, the Siemens motion control system, Simotion, might be the best choice. Simotion provides for both standard automation tasks and motion control tasks, like with Siemens PLCs. However, Simotion has one key advantage over PLCs – the Simotion Kernel.
The Simotion Kernel is the runtime system operating in the background on Simotion CPUs, and natively handles execution of motion tasks in parallel when demanded by the program logic. This results in both high performance and easy programming. Motion commands are simply called, with the details (acceleration, sync method, etc) specified easily through a graphical interface. Diagnostics are also baked into the kernel, allowing motion errors to be reported on a Siemens HMI with the tick of a box.
CNC Design has had great success in assisting OEMs develop solutions with Simotion for their motion-oriented machines. Simotion controllers offer native IP protection for OEMs, because they run compiled code that cannot be uploaded and reverse-engineered. OEMs also benefit from the OOP (Object-Oriented Programming) and library features of the Simotion Scout engineering software.
CNC Controller
FIGURE 7: Siemens Sinumerik HMI and Machine Control Panel - Connected to Sinumerik One - the Digital Native CNC Controller from Siemens
A common misconception is that CNC controllers are just for machine tools, and shouldn’t be used for production machines. This is not correct. Siemens Sinumerik CNC controllers, especially at the high-end, provide a ready-to-use platform for all kinds of motion automation tasks. If a machine requires accurate cartesian (X, Y, Z) positioning and/or cyclic patterns of motion, a CNC controller may be the best choice. Sinumerik has the following built-in features:
· Ready-to-use HMI for easy commissioning and operation of the machine.
· G-code language for easily programming of sequential or cyclic motion tasks.
· Built-in recipe management system (i.e. part programs).
· Native coordinate system awareness (similar to robots) – WCS, MCS (Work/Machine Coordinate System).
· Highly scalable with support for dozens of axes.
· A built-in PLC for handling safety and ancillary controls on the machine.
The CNC Design group is the exclusive agent for Sinumerik CNC systems in the Asia-Pacific region. With over 150 staff in several countries, CNC Design group has extensive infrastructure in place to ensure success with end-users’ and OEMs’ Sinumerik solutions. CNC Design has, of course, used Sinumerik successfully in many machine tool applications. However, Sinumerik has also been used successfully in other machines, such as:
· CNC Design’s GEARTest gearbox testing solution. The patterns involved in the gearbox testing cycle were particularly suited to Sinumerik.
· Wire mesh welders.
· Materials handling and stacking solutions – where X, Y, Z co-ordinates are required with reasonable precision.
· Motor core winders for Fisher & Paykel appliances. See (Case Study: Motor Core Winders).
In these applications, engineering time was slashed by avoiding the need to develop a motion control solution from scratch – instead, pre-existing features of Sinumerik were simply configured, and the required motion patterns specified with G-code.
Conclusion
You can automate any production machine with enough effort and money. However, to implement a simple, cost-effective and maintainable control system requires the right architecture. Obviously, this involves much more than selecting the right controller. Siemens’ broad range of selection across controllers, drives and HMI systems allows you to craft a well-fitting solution. As a motion control specialist and Siemens Solution Partner, CNC Design is well placed to partner with OEMs through the entire journey from specification through to life cycle services. That is exactly what we have done for many OEMs in New Zealand. Contact CNC Design today to discuss your application.